Paper History
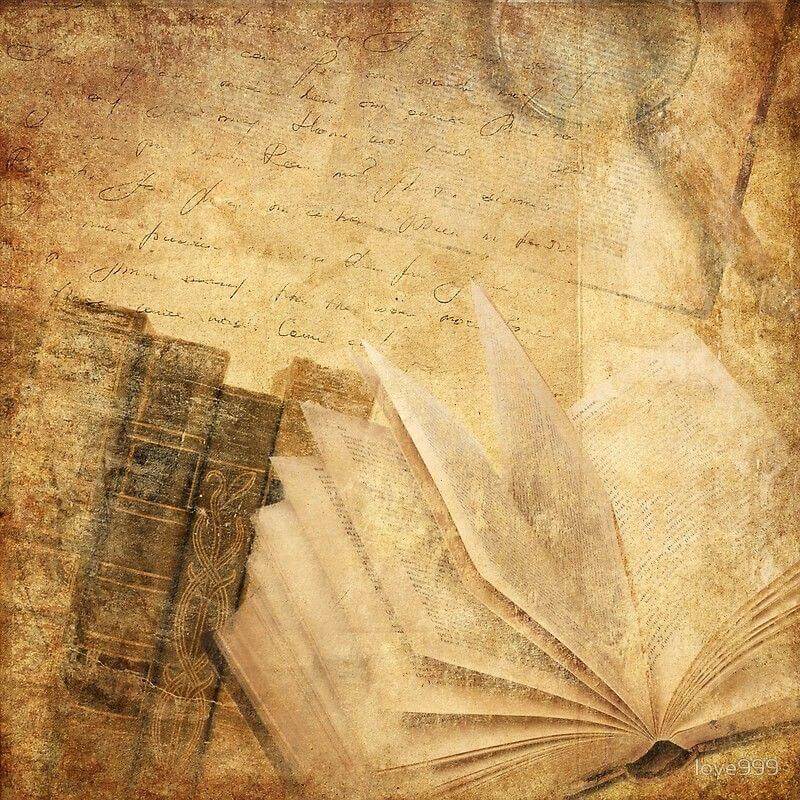
Who Invented Paper? : History Of Paper And Ink In India
Who Invented Paper? Do you know that paper was first invented in India? The age old perception that Paper was invented in China is not true. Find out the real fact? The popular and the known notion as to Who Invented Paper, points toward the Chinese inventors Cai Lun who lived between 50 and 120 AD. In the kingdom of the Eastern Han Dynasty in Guiyang, his first experiment with paper is established.
Another notion points invention of paper in India.
The established opinion holds that paper – specifically, Kurasani paper – was introduced to India in the eighth century by Arabs who had learnt the art from Chinese prisoners at Samarkand. Another view is of a Nepal-route between the seventh and ninth centuries. All these euphorias about Who Invented Paper is baseless and misinformed.
The TRUTH is the process of manufacturing paper originates from India and it spread world wide from there.
Who Invented Paper?
The indigenous methods of paper manufacture in the states of Maharashtra and Bihar were noted by many in the centuries that followed. The question that Who Invented Paper finds its answer right at this place.
If you go back to the history of the procedures of paper manufacturing you will witness you will notice the age old truth.
In the former state, a wooden block was fixed at the centre of an 8-foot diameter shallow well. Over several days, bark, hay, rugs, tents and gunny bags were moistened or soaked as per requirement. These were then placed on the central wood and beaten to a pulp with a beater. This pulp was subsequently placed in lime water (chunamed) reservoirs with a little water, and gum of the babul tree was dissolved into the mixture. Bamboo moulds were inserted and the material that adhered was lifted out and dried to form paper.
In Bihar, the materials were beaten with a wooden instrument called a dhenki, and then bleached, using soda water. The total was washed, next, and the procedure repeated six times. After this, the pulp was placed in a water-containing cistern and well-stirred. An hour later, the material was cut up into sheets (of paper).
Paper has a long history, beginning with the ancient Egyptians and continuing to the present day. For thousands of years, hand-made methods dominated and then, during the 19th century, paper production became industrialized. Originally intended purely for writing and printing purposes, a wide variety of paper grades and uses are now available to the consumer.
3000 BC
Of all the writing and drawing materials that people have employed down the ages, paper is the most widely used around the world. Its name derives from papyrus the material used by the ancient Egyptians, Greeks and Romans. Papyrus, however, is only one of the predecessors of paper that together are known by the generic term ‘tapa’ and are mostly made from the inner bark of paper mulberry, fig and daphne. Tapa has been found extensively in nearly all cultures along the Equatorial belt and is made by what is possibly the oldest papermaking technique – one still practiced in some parts of the Himalayas and South East Asia. Indeed, recent archaeological excavations in China have revealed some of the oldest ‘tapa’ paper ever found which shows that paper was being produced in China before western records began. The tapa technique involves cooked bast, which is flattened with a wooden hammer to form a thin, fibrous layer and then dissolved in a vat with water to make a pulp. A screen consisting of a wooden frame with a fabric base is then laid in a puddle or big basin and floats with the fabric just under the surface of the water. The papermaker then pours the quantity of pulp needed to make one sheet into this ‘floating mould’ and spreads it evenly, by hand, across the surface. The screen is then carefully lifted out of the water, allowed to drain off and a sheet of paper forms on the wire. Once the water has dripped off, the screen is placed in the sun or near a fire to dry. When dry, the sheet easily peels off and, apart from possible smoothing, requires no further treatment. This technique has two basic drawbacks. Firstly, a separate screen is needed for each new sheet, and is only available for use again after the last sheet has dried. And secondly, an increase in production can soon lead to a shortage of raw material, since fresh bast is not always available everywhere in the required quantity. The fibers normally used for textiles, like flax and hemp, also served as substitutes for bast. In later times, the fabric was replaced by fine bamboo sticks, which freed the papermaker of the need to let the paper dry naturally in the mould, since the poured or ladled sheet could be ‘couched’ off.
AD 105
In AD 105, the Chinese court official, Ts’ai Lun, (if we are to believe the chronicle recording the claim) invented papermaking from textile waste using rags. This can be considered as the birth of paper as we know it today. Later, Chinese papermakers developed a number of specialties such as sized, coated and dyed paper, and paper protected against ravages by insects, but they had great problems satisfying the growing demand for paper for governmental administration. They also used a new fiber-yielding plant – bamboo – which they de-fibred by cooking in lye.
AD 610
Chinese papermaking techniques reached Korea at an early date and were introduced to Japan in the year 610. In these two countries, paper is still made by hand on a large scale in the old tradition, preferably from the fresh bast fibers of the mulberry tree (kozo in Japanese). Following the cooking process, the long, uncut fibers are merely prepared by beating, which gives the paper its characteristic look and excellent quality. The latter is due, among other things, to multiple, rapid immersions of the mould, which results in a multi-layer fiber mat. Very soon, knowledge of papermaking spread to Central Asia and Tibet and then on to India. When the Arabs, in the course of their eastern expansion, neared Samarkan they too became acquainted with the production of paper and paper mills were subsequently set up in Baghdad, Damascus and Cairo, and later in Morocco, Spain and Sicily. Owing to the lack of fresh fibers, the raw material used by the Arabs was made almost entirely from rags: however, their defective and poorly designed processing equipment (such as breaker mills) produced a rather inferior ground pulp. But, by using this method, with screens made of reeds, thin sheets were made and then ‘coated’ with starch paste. This gave Arabian paper its good writing properties and fine appearance. The export of Arabian-made paper, along with the secrets of its product.
14 CENTURY
In the course of the rapid expansion of trade in the late Middle Ages, more and more merchants dealt in the commodity called ‘paper’ that was growing in importance for public and intellectual life. The Nuremberg councillor Ulmann Stromer (Stromeir) mulled over the advantages of making his own paper and, with the help of skilled workers from Italy, transformed the ‘Gleismühle’ by the gates of his home town into a paper mill. The dates noted in his diary, 24 June 1390 (start of work on the waterwheel) and 7 and 11 August 1390 (oaths sworn by his Nuremberg foremen), are the first assured records of papermaking on German soil. The wording of Stromer’s diary entries suggest that he regarded papermaking as a largely unknown and secret art, that he had to prevail against the clan of immigrant Italians, and that he had to overcome many technical difficulties. Stromer’s mill – illustrated in the world chronicle of Hartmann Schedel in 1493 – was initially designed with two waterwheels, 18 stamping hammers (i.e. six holes) and 12 workers using one or two vats.
16 CENTURY
The advantages of this mill-based papermaking technique, which spread throughout Europe in the 15th and 16th centuries far outweighed the disadvantage of considerable outlays of time and capital for building and fitting out with new machinery and equipment. However, the change in the production process, thanks to the division of labour, boosted output and improved quality. And it could certainly generate a profit, as some examples prove. On the other hand, there was a growing risk of an imbalance between costs and earnings, a state of affairs noted in the numerous reports of business failures among papermakers. Later, many paper merchants took over the mills as owners, while the master papermakers practiced their trade as lessees. This trend was stepped up by the special conditions prevailing in the book sector, where a book printer or publisher had to fund the production costs (paper, composition, and printing) of a work before the sale of the print run generated revenue. The result was that he was often indebted to the paper suppliers. Work at the vat normally involved four people: the vatman, who made the sheet using a mould; the couch squirt, who worked in time with the vatman and placed the sheet on felt; the layman, who drew off the still moist sheets from the felt after pressing; and the apprentice, who had to feed material to the vat and provide for vat heating. The press was operated jointly by the team. Depending on format and basis weight, up to nine reams (4,500 sheets) of paper could be made in the course of a working day of around 13 hours.
17 CENTURY
Technical progress continued in the 17th century. Smoothing the sheets by hand, using a creasing knife or ‘blood stone’, was supplemented by the use of a smoothing hammer (similar to a forging hammer). This led to a split in the craft between the tradition-conscious ‘smoothers’ and the modern ‘stampers’ who refused to recognize one another as fully-fledged papermakers. Towards the end of the 17th century, a new and much more efficient beater, called a ‘hollander’, was invented. This supplemented, or even replaced the stamping mill and further divided papermakers into two new camps. The tremendous upsurge in papermaking during the Reformation in the 16th century, coupled with the introduction of printing with movable type, soon led to a serious shortage of raw materials and to regulations governing the trade in rags. The systematic search for substitute materials met with little immediate success. In the early 18th century straw was certainly used as a raw material but failed to make headway on quality grounds. Only the invention of ground wood pulp by Saxon Keller (1843) and of chemical pulp (first patented in 1854 by Mellier Watt) solved this problem.
18 CENTURY
During the 18th century there had been some concentration of craft activities in large operations, the ‘manufactories’, which were dependent on skilled papermakers organised into craft groups. The efforts made to step up production as much as possible and to have many of the jobs done by machine (partly to get round the constraining rules of papermakers’ craft ‘usages’) culminated in the design and construction of paper making machines. The initial model was the vat that was used by J.N.L. Robert, who built the first flat-screen papermaking machine in 1798. This was further developed in England, mostly by Donking and the Fourdrinier brothers. Shortly afterwards other types appeared, like the Dickinson’s cylinder machine, and machines which filled wire moulds transported on an endless chain and couched the sheets on an continuous felt. Flat screen and cylinder machines, which were first seen in the 19th century, were continually improved and extended to include a dryer section. This soon led to a considerable widening of the paper web and to an increase in production speeds. It also heralded industrialization. In this new era, the small operators who were unable or unwilling to afford machines sought to survive with piece-work or by producing special grades, but they were sooner or later compelled to discontinue their activities. Others had to adapt their existing buildings or set up new mills elsewhere.
19 & 20 CENTURY
The history of the paper industry in the 19th and 20th centuries can be broken down into five partly overlapping periods, each marked by definite trends. In the first stage (from about 1800 to 1860), all work sequences previously performed by hand were mechanized. This included the rag preparation, the use of fillers, pulp beating, the paper machine with its various parts, and the machines required for finishing the paper (the head box, wire section, press section, dryer section, and units for reeling, smoothing and packaging). During the second stage (about 1840 to 1880), efforts were made to obtain rag substitutes on an industrial scale (ground wood pulp and chemical pulp) and appropriate industrial plants (ground wood and chemical pulp mills) were developed. The third stage (1860 to 1950) was marked by the enlargement of the web width, an increase in working speeds, the introduction of electric drive and further improvements to various machine parts. Machines designed specifically for the production of particular paper and board grades (for example the Yankee cylinder and multi-cylinder machines) were also developed. The web working width grew from 85 cm (1830) to 770 cm (1930), while production speeds rose from 5 m/min. (1820) to over 500 m/min. (1930). The fourth stage (1950 to 1980), which was still dependent on the old methods as far as the mechanics were concerned, brought unprecedented changes in papermaking. Alongside further increases in web width and working speeds, there was the use of new materials (thermo-mechanical pulp, deinked recovered paper, new fillers, processed chemicals and dyes), new sheet forming options (e.g. by twin-wire formers), neutral sizing, greater stress on ecology (closed loops) and, most of all, automation. The operational impact of these changes was: specialization in certain paper types; development of new paper grades (LWC – lightweight coated paper); corporate mergers; company groups with their own raw material supply and trading organizations; closure of unprofitable operations.
1980 ONWARDS
The fifth stage leads into the future. The evolution of new sheet-forming principles (with fluid boundaries between paper and non-woven fabrics) and chemical pulp processes have been the main process improvements. However, the situation on the global market (increased demand, above all in the Third World, trends in chemical pulp prices, problems of location), are again raising capital intensity and encouraging the formation of big company groups with international operations. At the same time there are definite opportunities for smaller, local firms satisfying specific needs.
2000 AND BEYOND
The new Millennium will be dominated by the tremendous progress that has been made in computer science, thus triggering a complete change in our commercial and private communication and information behavior. Does this mean that the paper era will come to an end? The answer is most definitely “No”. Clearly there will be a huge amount of data being generated electronically, but the issue is how to preserve it. The difficulties of data storage over a long period of time are well known (for example, the durability of disks; frequent changes of hard and software, electronic breakdowns etc.). Once again, paper offers the most convenient and durable storage option. The advance in technology will affect only the printing of items like short-lived handbooks and encyclopedias. Reading a book will remain a great pleasure into the future and paper, as a ubiquitous material with its many uses, will continue to play an influential role. Many artists will continue to express themselves by using this most versatile material.